There are many factors that can affect the service life of flexible metal hose. It is important to evaluate these factors for each hose application. Each individual application can be different than generally outlined applications. Shortened service life and even catastrophic failure can be avoided if the application conditions and individual hose assembly are well matched. The typical reasons for hose failure have been provided for design purposes.
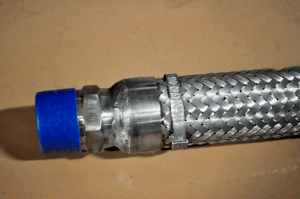
Universal Corrosion
Uniform corrosion would describe a uniform corrosion attack throughout the entire corrugated assembly. The chemical attack will be affected by the chemical concentration and the alloy of the corrugated hose. The bottom of the corrugation and the weld heat affected zone are prone to attack by corrosion. Hose alloy selection should encompass the review of the media to be transferred and the environmental conditions where the hose will be put into service to ensure correct compatibility. Consulting the Chemical Resistance Charts in the resources can aid in the selection of the correct flexible metal hose alloy.
Pitting Corrosion
Pitting corrosion is a form of localized corrosion that leads to a pinhole failure in the material. The area affected may have a surface defect like an inclusion or removal of the protective oxide layer. Typical pitting corrosion is usually the action of a galvanic reaction occurring in the pit of the corrosion. The damage usually occurs to the body of the material and is usually covered by the corrosion byproduct on the surface. The use of an alloy higher in Molybdenum 316L will typically increase the pitting resistance.
Intragranular Corrosion
Intergranular corrosion occurs in a metal alloy’s grain boundaries when they are more susceptible to corrosion than the larger inner grains. The grain boundaries become susceptible to corrosion due to a depleting mechanism that results in the formation of chromium carbide. The depletion of the chromium causes a once resistant metal to be affected by corrosion. Intergranular corrosion can also occur in the alloys of stainless steel when they are held at elevated temperatures exceeding 1000°F ~ 1562°F for an
extended period of time. The use of the stabilized stainless steel 321 or lower carbon stainless steels like 304L and 316L help increase the resistance to intergranular corrosion.
Steel Corrosion Cracking
The presences of tensile stresses and a chemical that is moderately corrosive to a particular alloy can lead to corrosion cracking. Parts can appear to be shiny and new in appearance while being filled with microscopic cracks. Stress corrosion can progress rapidly leading to catastrophic cracking ending up in failure of the part. Stress corrosion is more common in metal alloys than metals in their pure form. Failures due to stress corrosion cracking can be reduced by annealing parts after manufacturing to relieve any residual stress that may exist.
Fatigue
Fatigue is one of the most common causes of hose failure. It can be described as progressive damage due to the flexing of the corrugations. Stress generated by flexure, pulsation, torsion, vibration and flow induced vibration are some causes for fatigue failure. Fatigue cracks often begin at small imperfections, such as non-metallic inclusions, within the metal. Stress will concentrate at the crack and further cycling will increase the size of the crack until a complete fracture occurs. Fatigue damage can usually be seen as a circumferential crack at the top or bottom of the corrugation. Using a hose with a more favorable bend radius will decrease the stress level in the corrugations.
High Velocity of Media
As stated in Corrugated Hose Velocity Limits within this catalog, flow of a liquid or gas above certain velocity levels can result in premature fatigue failure. The high flow velocity causes the corrugations to vibrate at a high frequency. If the vibration is near the natural frequency of the hose, failure will occur very quickly. This type of failure is identified by spiderweb-type cracks and fractured pieces of metal breaking from the corrugations. Solutions would include reducing the velocity by increasing the hose diameter, reducing the bend of the hose or the use of an interlocked-type liner for smooth flow.
Vibration
Vibration damage starts as very small or irregular cracks close to vibration source. The cracks are typically located in the outer circumference of the corrugation. The cracks may propagate towards the walls of the corrugation in a shape of a “Y”. Signs of braid abrasion on the inner hose from excessive braid movement will be present. If the vibration frequency occurs at the natural frequency of the hose, failure will occur rapidly.
Pressure Rupture
Pressure rupture can occur when metal hose assemblies are subjected to constant or pulsating pressures greater than the design pressure of the hose. In cases of hose rupture, the braid fails and the inner hose is forced through the opening until the hose reaches its stress limits causing a tear or hole in the material. Hose selection should consider the temperature and pressure ranges the hose will be subjected to during service. Caution must be used when unbraided metal hose assemblies are used in low-pressure applications. Proper installation practices utilizing piping guides and anchors must be observed to prevent premature damage of the metal hose assembly. The addition of braid should be considered for vibration attenuation.
OnGuard Asset Tracker has Maintenance Programs to Improve Hose Safety
Reduce the risk of hose failures through routine hose inspections, testing and certification programs. Our OnGuard™® hose management services include testing, tagging and traceability of your hoses from “cradle to grave”. These proactive programs are managed by our hose experts and keep you running efficiently and safely.
